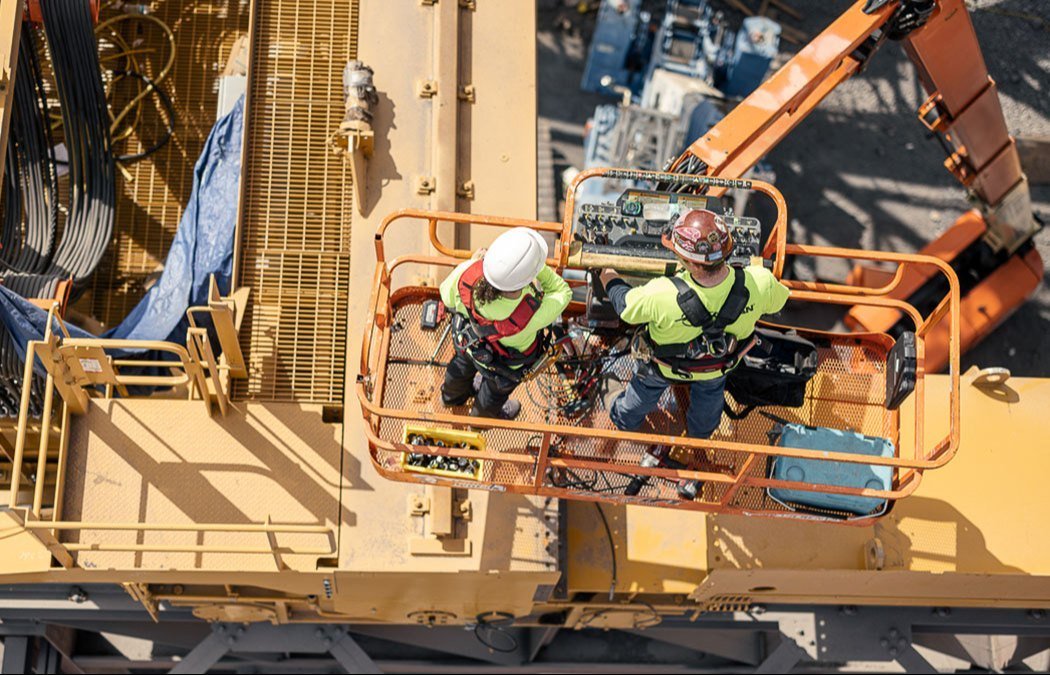
Services
AMC (Annual Maintenance Contract)
Annual Maintenance Contracts (AMC) and Predictive Maintenance are two key strategies used to ensure that cranes remain in optimal working condition, minimizing downtime, and reducing the risk of unexpected failures.
An Annual Maintenance Contract (AMC) is a service agreement between the crane owner and a maintenance provider (typically a manufacturer or service company) where the provider agrees to maintain the crane for a set period (usually one year). In return, the crane owner agrees to pay for maintenance services either on a scheduled or as-needed basis. AMCs are commonly used to ensure that cranes receive regular inspections, preventive maintenance, and necessary repairs.
Key Features of an AMC for Cranes
Scheduled Inspections: The contract usually includes routine, scheduled inspections and maintenance visits to ensure the crane is operating correctly. These inspections typically cover all vital components, such as mechanical systems, electrical systems, lifting mechanisms, and safety features.
Preventive Maintenance: Under the AMC, the crane is serviced according to the manufacturer’s recommendations to prevent breakdowns. This can include lubrication, parts replacement, alignment checks, calibration of sensors, and hydraulic fluid changes.
Repairs and Replacements: The AMC can cover repairs of defective or worn-out parts, such as the engine, electrical components, cables, or safety devices. Depending on the terms, it may cover parts replacement costs or provide discounts on parts and labor.
Emergency Support: Many AMCs offer 24/7 emergency support in case the crane breaks down unexpectedly. This service helps minimize downtime by getting the crane operational as soon as possible.
Cost Management: One of the main advantages of an AMC is cost predictability. Since the contract covers both preventive and reactive maintenance, it helps crane owners budget for maintenance costs over the year.
Benefits of an AMC for Cranes
- Minimized Downtime: Regular inspections and preventive maintenance help identify potential issues before they result in breakdowns, reducing downtime.
- Predictable Costs: Fixed annual fees make budgeting easier for crane owners and avoid unexpected repair bills.
- Expert Care: AMCs are typically handled by experienced and certified technicians, ensuring that the crane is serviced according to industry best practices and manufacturer specifications.
- Extended Crane Life: Regular maintenance can help extend the service life of the crane by ensuring that components are regularly inspected, lubricated, and replaced before they fail.
- Compliance with Regulations: Many jurisdictions require cranes to undergo regular inspections and maintenance to comply with safety regulations. An AMC ensures compliance with these standards.
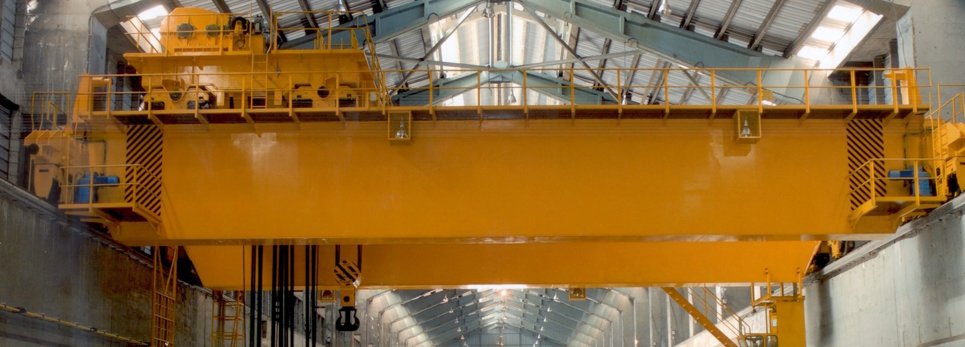
Types of AMCs
- Comprehensive AMC: Covers all aspects of crane maintenance, including labor, parts, repairs, and emergency services.
- Basic AMC: Covers only routine maintenance tasks, such as inspections, minor adjustments, and lubrication, but excludes repairs or part replacements.
- Customized AMC: Tailored to the specific needs of the crane and the operational environment. It may include specific services, such as more frequent inspections or additional coverage for particular crane components.
Predictive Maintenance for Cranes
Predictive Maintenance (PdM) refers to the use of data-driven technologies and advanced analytics to predict when and where maintenance should be performed on a crane. The idea is to address potential issues before they lead to failure, maximizing crane uptime and minimizing unnecessary maintenance activities. Predictive maintenance relies on real-time data collection, machine learning, and diagnostics to monitor crane performance.
Key Components of Predictive Maintenance in Cranes
- Vibration Monitoring: To detect wear and tear in moving components like motors, gearboxes, and bearings.
- Thermography: Using infrared cameras to monitor temperature changes in critical components, helping detect overheating or other issues.
- Oil and Fluid Analysis: Monitoring the quality and condition of hydraulic fluid, lubricants, or engine oil to detect contamination or degradation.
- Load Monitoring: Ensuring the crane is not being overloaded by continuously monitoring the weight of the lifted load.
- Pressure and Temperature Sensors: These sensors help monitor hydraulic pressure, engine temperature, and other key factors that can indicate potential problems.
Technologies Used in Predictive Maintenance
- Internet of Things (IoT): Sensors and smart devices on cranes collect data continuously, feeding into cloud-based platforms for analysis.
- Machine Learning (ML) and AI: These technologies help analyze vast amounts of data and build predictive models that forecast when a component will fail or require maintenance.
- Big Data Analytics: The data collected from cranes and operational conditions is processed and analyzed in real-time to detect anomalies.
- Remote Monitoring: Technicians and operators can monitor the crane’s health remotely, gaining insights into its condition without being physically present.